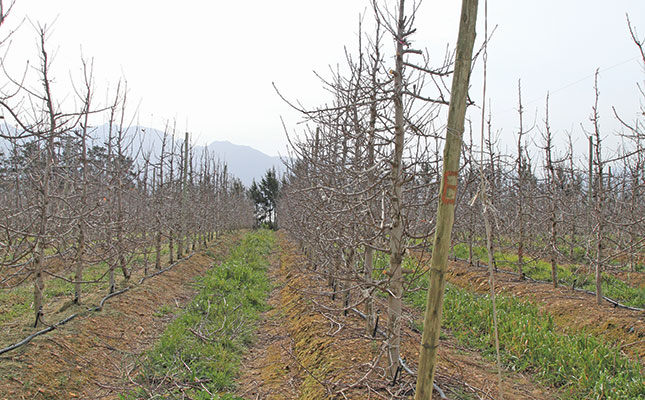
Photo: Glenneis Kriel
When the three Lingenfelder brothers, Albert, Guillaume and Francois, joined their family fruit farm near Villiersdorp in the Western Cape in 1995, 2002 and 2004 respectively, they were disappointed about the yield per hectare of apples and pears.
In 2008, they joined Two-a-Day Group, and the then technical team, headed by Dr Mias Pretorius, went out of its way to help the brothers increase their tonnages of apples in particular. Today, their farm, Rustfontein, produces 75% more crates of apples than in earlier years, and is amongst the top 5% of suppliers to Fruitways, a specialist marketer of apples and pears.

The Lingenfelders’ technical adviser, Anton Muller, also has a major influence on their success.
“Anton has vast industry experience and is a top specialist in his field. We work well with him, because we share the same vision and production philosophy,” says Albert.
High-density planting
Albert identifies the switch from traditional to higher planting densities as one of their main game changers. The first apple trees on the farm were planted at 5m x 3m intervals in 1978, and this was reduced over time to 4,5m x 1,5m, and then to 3,5m x 1,5m in 2016.
“Instead of 666 trees/ha, we now have 1 905 trees/ ha, allowing us to maximise income, while using our land, water and other resources, such as pumps, farm implements and labour, more efficiently,” he explains.
The farm has 110ha planted to apples and 36ha to pear trees, with about one-third of the apple orchards so far being planted at high density.
Guillaume encountered the results of high-density planting first-hand in 2016 when he accompanied Two-a-Day’s technical team to Bolzano, Saluzzo and South Tyrol in Italy to study how the Italians farmed apples.
“I was so impressed that I phoned my brothers from an orchard in Italy and told them to stop planting an orchard they were ridging, and instead plant at high density using the production system I’d seen,” recalls Guillaume.
The Lingenfelders became the first farmers in the Villiersdorp and Vyeboom areas to plant this way, using the spindle and ‘double-railtrack’ systems. The first of these soon became their preferred method, explains Guillaume, as the railtrack system cost almost R25 000/ ha more.
This was because it has 16 wires on which 32 branches of each tree are trained, whereas the spindle system uses only three wires to support the trees, which are shaped like tall spindles.
Having more branches to train, the railtrack system also requires far more labour to shape the trees during the first few years of production.
In both systems, however, the trees, once shaped, are easier to spray, manage and pick than traditional trees. This is thanks to their shallower depth and the fact that the branches are manipulated to be softer and thus easier to work with. According to Albert, the man hours required to pick and prune these trees is less than half of what it takes for trees planted at lower densities.
“With high-density planting, we bend fewer than a quarter of the number of branches than in the case of lower-density planting. To do this, we prune the trees as late as possible, once the branches start to turn green, or even during flowering when working with vigorous growers. This results in softer shoots that don’t need to be bound.”
With lower-density orchards (4,5m x 1,5m), the branches are removed in winter to create stronger, stiffer shoots with the ability to fill the larger area taken up by these trees.
Albert explains that they are gradually doing away with the practice of pruning with shears and instead removing unwanted branches that threaten to overshadow others.
Battery-operated saws are used for this purpose. This results in better light penetration between the branches, which in turn improves the size, colour and quality of the fruit, and produces higher packout rates. In addition, the trees reach commercial production volumes almost a year earlier than those planted and pruned in the traditional way.
Guillaume recalls that many farmers visited the orchards on Rustfontein after the brothers converted to high-density planting and expressed doubt that this approach would be profitable.
“The shift from traditional big trees to these small, thin trees was too much for them. They said the rows were too narrow, we wouldn’t be able to pick and work the trees, and the trees wouldn’t be able to carry heavy loads. Today, however, high-density planting has become the new norm, with farmers who don’t do it struggling to remain competitive,” he says.
Rootstocks
Rootstocks are a key enabler of planting at high density, but, as Albert explains, this has not been an entirely straightforward process.
Due to the high clay component and poor quality of their soil, they required a more vigorous rootstock than the well-known M9 dwarfing type. Geneva rootstocks were not yet available in South Africa, however, so they settled for MM109, which provides better growth than the dwarfing rootstocks.
Their plan is to switch to the Geneva 778 rootstock for new plantings, as this is more fertile than MM109 as well as being vigorous. It is also resistant to certain soil-borne diseases, such as apple replant disease and Phytophtera.
Mechanisation
The adoption of new technology has been another game changer. “When new technology becomes available, we want to be the first to try it out. So we invite companies to experiment with their new products on our farm, as this gives us an idea of what’s happening and whether the products would work under our conditions,” says Guillaume.
This started with the importing of a pruning platform 10 years ago to mechanise the manipulation of young trees. Two people standing on the platform to work on the trees while it moves through the orchard, enables them to achieve the output of 12 people during the same time frame.
The next purchase of note was battery-powered Pellenc saws. As with the platform, two workers operating these saws are as productive as 10 to 12 people cutting branches by hand.
Albert adds that the saws also enable them to employ specialists to do the manipulation work.
“This is complicated and training takes a long time. Mistakes are expensive and reduce the quality and quantity of fruit produced by a tree.
“The workers who manipulate our trees grew up on the farm and are specialists in their jobs. They know exactly which branches to remove and what method to follow when manipulating trees in each orchard,” says Albert.
The batteries of the saws last for a day, and have to be recharged at night. The blades are replaced after two weeks.
Battery-operated shears are another improvement, as they enable a team to get the job done far faster than with ordinary shears. These shears work with a trigger, so good management is needed to avoid mistakes.
“Each of us is responsible for a team of pruners,” explains Albert. “We explain to the team manager what we want and then check up on the team a little later to see if they’re doing the work properly, or if the pruning should be tweaked.”
For the past six years, draped nets have been used on the farm to improve apple quality. White nets are used to improve the colour of high-value bicoloured varieties such as Fuji Supreme, while black nets are used to protect green varieties such as Granny Smith against sunburn.
The nets, which last about 10 years, are draped over the trees once fruit set starts. Guillaume says, however, that production volumes of the green apple varieties appear to have decreased since they started using the nets a few years ago, and they are therefore considering using them on these varieties only every alternate year.
Precision farming
The Lingenfelders started using precision fertilisation two years ago, and have since seen significant gains in fertiliser-use efficiency.
Albert explains that they used to take one soil sample per hectare every three years after the harvest in order to measure nutritional imbalances, and this was followed by blanket fertiliser applications to rectify the imbalances. But this resulted in over-fertilisation in some areas, and under-fertilisation elsewhere.
With precision fertilisation, samples are taken from four holes per hectare. The fertiliser is then applied at variable rates, according to the results, with a Red Ant precision fertiliser spreader. A GPS-based system is used to ensure that the sample holes are dug in the same spots each time.
Because of the high cost of soluble fertiliser, only 10% is supplied by fertigation with drip irrigation. The rest is applied with a precision fertiliser spreader.
The fertilisation programme is based on the trees’ nutritional requirements at different growth stages, as well as the quantity of fruit borne in summer. Additional fertiliser is applied after harvesting according to the yield produced.
Along with this, the Lingenfelders acquired Rovic Leers’ tower blowers to apply fungicides. These not only provide better spray coverage, but save water and time. The sprayer moves at about 6km/h and uses around 500ℓ water/ ha, in comparison with Rustfontein’s old sprayer, which moved at 3,2km/h and used 750ℓ water/ha, according to Guillaume.
While the drought of three years ago was challenging, it also provided a learning curve, adds Albert.
“People used to believe that apple orchards required at least 7 500ℓ water/ ha/ season, but we managed to get away with 4 500ℓ water/ha/season, without this having a negative impact on fruit quality.”
DFM probes are used to measure soil moisture levels throughout the day, and Albert checks these readings at least three times a day from November to May to prevent over- or under-irrigation.
The water is delivered via short-range micro-sprinklers, while 10% of the farm, consisting mostly of new high-density plantings, is covered by double-dripper lines, which are used to ensure that enough water is delivered on hot days.
Albert adds that additional water is supplied to the trees a day or two before a heatwave is expected, in order to regulate the moisture content of the soil and prevent damage to the plants.
The brothers try to irrigate most of the orchards at night, when evaporation is low. During the day, water managers walk through each orchard at least once a week to check the irrigation system for problems, such as breakages or blockages.
To save electricity costs, water is pumped only during Eskom’s off-peak hours, and variable speed drive pumps have been fitted. Water is pumped into a dam that feeds the orchards via gravity.
Mechanising pre-sorting
In 2012, the brothers took a big step forward with the purchase of a pre-sorter for the packhouse, and this was followed by another in 2021.
This, explains Francois, has not only significantly reduced the number of sorters per picking team, but streamlined the entire process, with pre-sorting and sorting now taking place under one roof.
In addition, rather than working outside, where the midsummer temperature can reach 40°C, employees involved in pre-sorting can do their job in a more comfortable and efficient environment that allows them to identify blemishes and sunburn more easily.
On top of this, the pre-sorter has enabled Rustfontein to improve earnings for Grade 1 and Grade 2,5 apples. Francois explains that other grades of fruit used to end up with the Grade 1 fruit, which drove up the storage cost of the fruit. Apples are sometimes stored for up to nine months before being exported, he explains.
In the past, all the apples that did not make export grade were sent to the juice market, but Grade 2,5 apples are now separated during sorting and sold to an informal trader.
The farm earns approximately R400 more for a 348kg crate of apples on the informal market than in the juicing market.
The first pre-sorter paid for itself within two years, but Francois says it will take much longer for the new one to realise a return on investment, as the prices of pre-sorters have skyrocketed over the past decade, whereas apple prices have come under pressure in the informal market.
While farming with family can be challenging at times, the three brothers are satisfied that they make a good team. They say they give each other room to thrive in their own management divisions and, crucially, they share a common goal, which is to make the farm as great as it can be.
Email the Lingenfelder brothers at [email protected], [email protected],
or [email protected].